The field of Nondestructive Testing (NDT) plays a critical role in ensuring the structural integrity and fitness for service of various industrial equipment. Among the various NDT methods, Ultrasonic Thickness Testing (UTT) is a widely used technique for assessing the thickness of materials in equipment such as pipelines, pressure vessels, and storage tanks. In this blog post, we will emphasize the importance of consistent inspection point locations or UT thickness locations in the overall fitness for service or integrity analysis of equipment. We'll explore the various applications of UTT and discuss factors that can affect the accuracy and precision of measurements, including the role of NDT Seals' inspection point labels and the ISQ for UTT from ASNT.
APPLICATIONS OF UTT
Ultrasonic Thickness Testing is a versatile technique used in various industries, including oil and gas, petrochemical, aerospace, and manufacturing. Some of the key applications of UTT include:
-
Corrosion Assessment: UTT is employed to measure the remaining wall thickness of equipment to detect and quantify corrosion or erosion, allowing for timely maintenance and integrity management.
-
Material Integrity: It is crucial for assessing the structural integrity of components like pressure vessels, storage tanks, and pipelines, ensuring they can safely withstand their intended operating conditions.
-
Weld Inspection: UTT can be used to verify the thickness of welds to ensure they meet design specifications and standards.
-
Safety and Regulatory Compliance: Regular UTT inspections help organizations comply with safety and regulatory requirements by identifying thickness deviations that may compromise equipment integrity.
IMPORTANCE OF CONSISTENT INSPECTION POINT LOCATIONS
Consistency in inspection point locations or UT thickness measurement locations is vital for reliable and meaningful results in UTT. Here's why:
-
Data Repeatability: Consistency ensures that measurements taken over time are comparable, making it easier to track material degradation or changes in thickness due to various factors.
-
Accurate Analysis: Accurate location data is essential for fitness for service assessments. Deviations in inspection point locations can lead to inaccurate conclusions about equipment integrity.
-
Inspection Planning: Consistent inspection locations simplify the planning and execution of inspection programs, ensuring that all critical areas are examined.
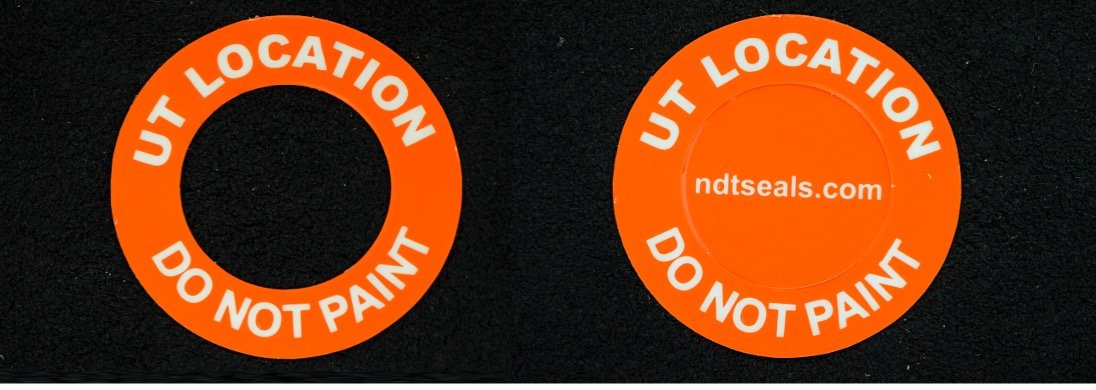
FACTORS AFFECTING ACCURACY AND PRECISION
Several factors can influence the accuracy and precision of UTT measurements:
-
Inspection Point Labels: NDT Seals' inspection point labels help ensure that inspection points are consistently located. These labels provide a visual guide for technicians, reducing the likelihood of errors due to human judgment or memory. Their low-leachable adhesive and their stability at temperatures from -40°F to +300°F make thickness measurement locations one less thing to worry about during the analysis.
-
Technician Skills: The competence of the technician conducting UTT is crucial. The American Society for Nondestructive Testing (ASNT) has introduced the ISQ for UTT, a certification program that sets industry standards for technician qualifications and implements a hands-on exam for certification. Skilled technicians are less likely to make errors and can interpret data accurately.
-
Calibration: Proper calibration of equipment is necessary to ensure accurate measurements. Regular calibration checks should be performed to maintain equipment accuracy. Quality calibration blocks of the right material and for a given application are also important to achieve proper calibration.
-
Surface Conditions: Surface conditions, such as roughness or coatings, can affect measurement accuracy. Technicians must prepare the surface adequately to obtain precise results.
Ultrasonic Thickness Testing is often viewed as an “easy” NDT method however there are many factors that can affect its accuracy. UTT is a valuable tool for assessing equipment integrity and ensuring safety in various industries. The consistency of inspection point locations or UT thickness measurement locations is paramount to the accuracy and reliability of UTT results. Using inspection point labels from NDT Seals and certified technicians with ISQ qualifications from ASNT can help maintain accuracy and precision in measurements. With these measures in place, organizations can confidently assess the fitness for service of their equipment, reduce downtime, and enhance overall safety and compliance.
By recognizing the significance of consistent inspection point locations, industries can ensure the longevity and reliability of their critical equipment, ultimately preventing costly failures and ensuring the safety of personnel and the environment.